You may find yourself welding on the weekend with your trusty mig welding machine but something just isn’t right. You are getting lots of welding spatter and your best mate, the welding guru is out of town, what do you do? Well there are a few things that can be undertaken to remedy the situation.
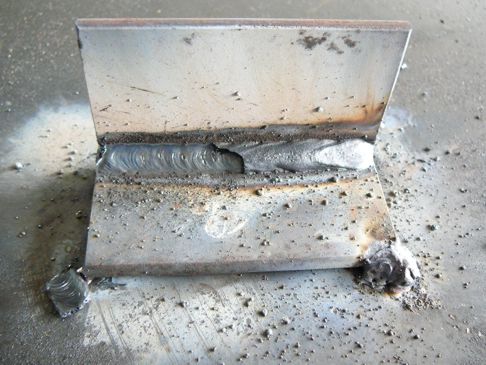
Mig welding spatter is bad
1. Increase the MIG welding voltage
Try to reduce the spatter by adjusting the voltage of the machine. Voltage is closely linked to the welding arc’s length and the heat input of the weld. Find the right balance, so the weld is being created with the correct intensity.
2. Change The Welding Torch Angle
Keeping the position of your welding gun with the wire in front may make a nice, smooth weld, but it shoots spatter outward. A drag angle with the wire behind, keeps spatter in the weld pool.
3. The 3 C’s, Clean Clean Clean the weld surface
The easiest but most overlooked way to avoid spatter is to keep your welding surface free from contamination. Substances like oil may cause the welding power supply to alter the machines parameters settings – creating spatter before and after the right adjustments are made.
Anything that may oxidize the weld pool such as rust may create bubbles that burst, generating even more spatter. It is advisable to clean the surface and avoid the mess. Remove any build-up with an abrasive tool/brush or chemical.
4. Shielding Gas and Wire
The shielding gas and welding wire should be preventing spatter, not contributing to it. Argon gas can minimize spatter, but it can alter other aspects of the weldment. Many wires contain deoxidizing substances, which will reduce the amount of spatter. Flux cored wires are considered an excellent safeguard against spatter. Reducing the wire feed speed can help overcome the problem of excessive spatter.
If this isn’t effective, the excessive spatter may be the result of arc blow that occurs when magnetism in your base metal affects the quality of your arc. To combat arc blow, try welding toward your work return clamp.
5. Shelter the Welding Environment
In the battle against spatter, wind is considered an enemy. Ensure the shielding gas isn’t being affected by air flow. Another environmental problem that causes spatter, cable grounding, can be easily fixed. Make sure cabling is secure and on clean surfaces, otherwise, you may have weld altercations.
6. Anti Spatter Spray
To prevent weld spatter build-up it is advisable to invest in a high performance anti spatter spray to protect against spatter adhesion on jigs, fixings, mig nozzles, welding equipment, work pieces and surfaces. Simply apply prior to welding for maximum spatter protection. Be careful not to spray too much anti-spatter onto the weld joint itself. The anti-spatter can cause small defects in the weld that look like pinholes. This is known as porosity and it reduces the strength of the welded joint.