Synergic Mig Welders
Synergic Mig Welders are a variation to pulsed Mig welders. A synergic welder provides incremental current pulses which form small droplets of similar sized molten material on the tip of the welding wire combined with the other specific relationships necessary for stable wire burn off. These droplets detach and fall into the weld pool. Incremental current pulses are unique to a given material and wire diameter and their details are programmed into the synergic welder control board. Modern sets contain a variety of consumable and wire diameter combinations, including programmes for flux and metal-cored consumables.
The three essential characteristics of synergic operation are:
- Pulse parameters are selected automatically.
- Pulse frequency or duration is directly related to wire feed rate.
- Electronic control of parameters ensures uniform penetration and weld bead profile.
In practical terms, this allows an operator to pre-select wire material and diameter once for any welding operation, then adjust the one control that governs wire feed rate. The ‘one knob’ operation synonymous with this type of power source is the principal advantage of such a system compared to conventional non-synergic sets, which require that the pulse parameters (pulse frequency, peak/background current etc.) be individually set for a given wire feed speed. Thus synergic welding sets offer the advantages associated with pulsed MIG/MAG welding, combined with a ‘welder friendly’ control system.
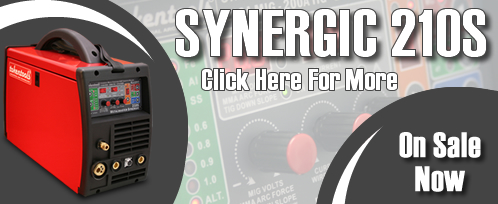
Tokentools Metalmaster Synergic Mig Welder
Synergic welding control is also used in conventional MIG/MAG, in which the voltage is adjusted in relation to the wire feed. It is now possible to buy a ‘synergic wire feeder’ which performs this function in conjunction with a standard rectifier power source.
1 comment on “Synergic Mig Welders”